BROUGHT TO YOU IN COLLABORATION WITH METROPOLIS MAGAZINE
Alchemy Architects points to the future of modular housing
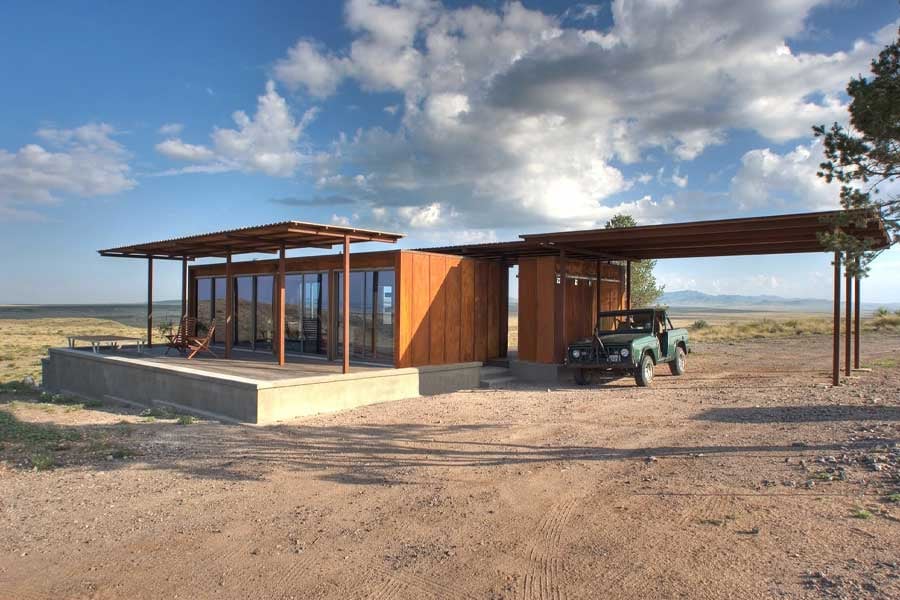
Prefabricated homes have long been touted as the solution to so many of the challenges facing housing. From affordability, to sustainability, to quality – the value prefab construction promises to dwellers is high. It makes sense then, that architects who are focused on these qualities would look to modular prefabrication techniques to make an impact. With a penchant for innovation, architect Geoffrey Warner found his way into the prefab movement early, and managed to turn an experimental one-off project into a popular iterative series of homes which are as energy efficient as they are attractive. Warner’s firm Alchemy Architects first created the weeHouse® as a customizable dwelling that showcases what Warner calls “the luxury of less.” Now he’s building a new project, dubbed the lightHouse, as a way to further popularize modular housing.
Based in St. Paul, Minnesota, the firm produced its first prefab dwelling in 2003 when a client asked Warner to build her a retreat on a rural plot of land in Wisconsin, for under $50,000. “We said you could have a pole barn—a big thing with nothing in it—or a jewel box with no plumbing or electricity that we would build ourselves in a warehouse. Everyone thought that the jewel box was the way to go,” he says. “It wasn’t a plan, it grew out of needing to solve a problem, and prefab was the tool we thought might be a way to do that, to save money and to save time.”
The result was the first weeHouse. Using an 8×8-foot patio door as the starting point around which factory-made walls and finishes were added, the streamlined house came in at 336 square feet with wood-wrapped walls, oil-stained floors, and floor-to-ceiling windows that embraced the landscape. After publication of the project, public interest was so strong that Warner went on to develop the weeHouse into a series of small light-filled modules which can be configured and fully customized based on client needs.
The project also prompted Warner to turn his attention more fully towards prefab techniques as a way of delivering quality housing to everyone, regardless of income level. As Warner points out, there were 92,000 manufactured homes delivered throughout the U.S. in 2017, but in his view “many of these fall short of the design and quality that is possible. Assuming that the goal is to make housing both high-quality and sustainable, how can we build it better and more cost efficiently? With prefab, you eliminate the uncertainties typical in the conventional construction process and it is a win for everyone involved,” he says.
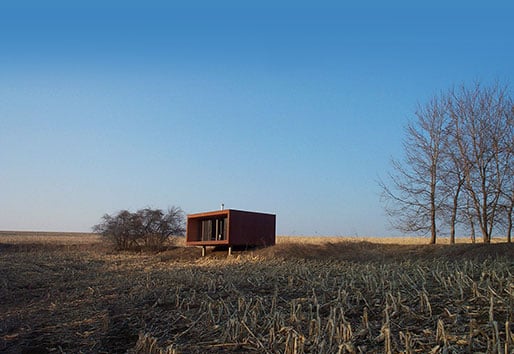
With this approach, over fifty weeHouses have been built across the country since that first one, many in rural areas where the ability to create a sleek little dwelling may otherwise be limited by materials and local expertise. The homes can be easily sized up or down—from 336 square feet to over 4,000—and are adaptable to any region. One San Diego-based client enthused that her windows, produced by Andersen Windows and Doors, were unbelievably quiet, which Warner attributes to the triple-glazing developed for Minnesota winters.
Inherently eco-conscious with their small sizes and smart building techniques—“the greenest square foot is the one you don’t build,” Warner quips— the weeHouses have only become more sustainable through continued improvements over the past fifteen years. “A lot more people have picked up on issues of energy use and carbon use to make more sustainable products and systems. We’ve been able to incorporate these features into our design work.” Recent weeHouse projects have included solar power, green roofs, passive heating/cooling, and hydronic underfloor heating, among other options.
Alchemy’s newest project, the lightHouse, is the next iteration that’s an even more affordable prefab option and can be easily replicated in dense urban settings. The 450-square-foot dwelling is designed to be prefabricated in a modular factory, made out of R-40 structurally insulated panels (SIPs), or stick-built on site. The system also incorporates Andersen® windows as a central element to let both natural light and views of the landscape flow in. The intent of the lightHouse is to “democratize the process so that more people can benefit from it. We wanted to design the hell out of something small to get a really beautiful project,” he says. Though it’s not customizable like the weeHouse, its low energy use, trim size, and modular configuration lends it to diverse solutions, from extended family apartments to rental units to guest houses. And it’s replicable at scale; there are currently rooftop communities under development using the lightHouse, as well as a half-city block in St. Paul.
Geoffrey Warner
Photos courtesy Alchemy Architects.