How to install a joined replacement window unit
In this Onsite with Andersen video, we’re following along as Minnesota Weatherization Systems installs a large, joined window unit in a historic home.
The takeaway: Details, details, details. While they’ll vary from one job to the next, coming with a plan will help you get them right at every step from preparing the rough opening to trimming the new window. Here, the crew were able to pull off a complex installation involving a large window unit requiring a non-standard approach — building a window buck. This was no accident. They understood the conditions and came prepared — get tips on how to assess for replacement.
Keep reading for a review of the steps involved in this installation, plus helpful tips that’ll help you nail your next job.
Review of the replacement installation
The joined unit shown in the video included four 400 Series Tilt-Wash Double-Hung Windows, which were being installed in a nearly 100-year-old brick home. The home’s facade required a window buck to be built so the full-frame flanged replacement unit could be fastened into the rough opening.
Here’s a summary of the steps the contracting company, Minnesota Weatherization Systems (MWS), followed:
Step by step
1. Removed the old windows, frames, and jambs
They needed to get down to the rough opening (RO) so they were working from a clean and strong surface upon which a buck could be built.
TIP: This replacement project was unique in that it used both new construction and replacement methods and techniques. Every install is different. You can get instructions customized to your product, installation method, and more when you use our Installation Guide Configurator.
2. Added low-expanding foam in between the brick facade and the RO
Once the old materials were out of the way, this step was taken to prevent water and air from penetrating into the home.
TIP: In a new construction scenario, the weather-resistive barrier (WRB) would be wrapped inside the rough opening. In this scenario, where the brick facade wasn't going to be removed, they need to take other steps, like filling gaps with low-expanding foam and building a buck that could be flashed.
3. Built bottom and sides of the window buck
TIP: The design of a buck will be specific to the project and could come from the architect, builder, or contractor.
4. Flashed the sill
Flashing the sill is always a critical step to proper installation. Flashing with a continuous piece of flex wrap along the bottom of the RO and buck and 6 to 8 inches up both sides, will give water a path out — should it ever penetrate. Flashing the buck is essential because it means the window will be connected to the WRB and not an exposed part of the RO. Straight flashing was used on the other sides.
TIP: This install crew included four people. Having two installers outside and two inside was helpful at various points because the unit was so large. For example, the crew on the outside were able to make sure the proper spacing was maintained between window frame and brick trim, while the crew inside checked for plumb, level, and square and installed shims.
5. Planned for brick mould
TIP: Shims are an installer's best friend, especially in a replacement project where the RO might not be perfectly square. They allow for more finite adjustment. We recommend horseshoe shims. They can be easily stacked, and their handles allow them to be placed at the proper depth and then snapped off.
6. Built top of the window buck
Dry fitting the window allowed them to determine how much space to leave for the top of the buck, while taking into account the nailing flange, brick mould, and any shimming that might be required. Checking for level in each of the four openings helped them to determine where shimming would be needed. With optimal sizing determined, they added the top member of the buck.
TIP: The crew removed the sashes from the window to make the unit lighter and more maneuverable for dry fitting and installation. Once the frame was installed, they went back and set the sashes into place.
7. Applied sealant over the holes in the nailing flange
This belt-and-suspenders approach means the sealant will be carried into the holes protecting these penetrations in the RO.
TIP: Sealant was applied while the frame was laying on the ground. This takes the guesswork out of the equation. Installers can see exactly where the installation holes are and cover them appropriately.
8. Inserted window frame
With the RO fully prepared and sealant applied to the nailing flange, they inserted the frame into the RO. They checked each opening for level and added shims where needed before fastening the frame.
TIP: The installation holes included in the nailing flange are not random. These holes are placed to make sure the window meets a certain performance grade — design pressure is a similar test of performance. Skipping fastening any of these holes could jeopardize your window’s performance.
9. Flashed window frame
Once the window frame was fastened and sashes were slid back in place, the crew added flashing over the nailing flange. They began at the bottom, did the sides and finally, the top — i.e., the shingling or lapping method. Flashing the flange helps prevent any wind-driven rain that might penetrate the brick mould from entering the rough opening.
TIP: When flashing, always follow the lapping or shingling technique. This means flashing begins at the bottom, is overlapped by the sides and finally the top. This is done to encourage water to follow gravity down and out, should it ever penetrate the opening.
Why 400 Series Double-Hung Windows?
There were several reasons this exact product was chosen, including:
- More glass overall: Replacing individual units with a joined unit that didn’t require structural framing in between each window allowed for 12-15" of additional glass.
- Forgiving installation: The compression jamb liners of 400 Series make this window ideal in a replacement scenario where ROs are not perfect. No matter if the RO is pickle barreled or hour glassed, the flexibility of these jambs allows the sashes to fit tightly in the frame.
- Easier maintenance: The top and bottom sashes of these windows both tilt in making them easy to clean from indoors. Additionally, the compression jamb liners can be removed if the balancers ever need to be adjusted.
More about this project
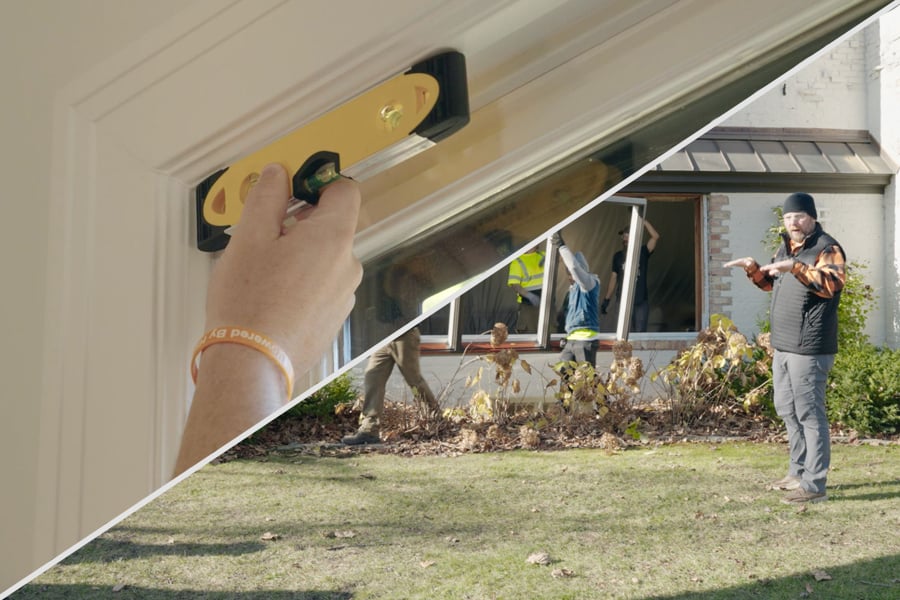